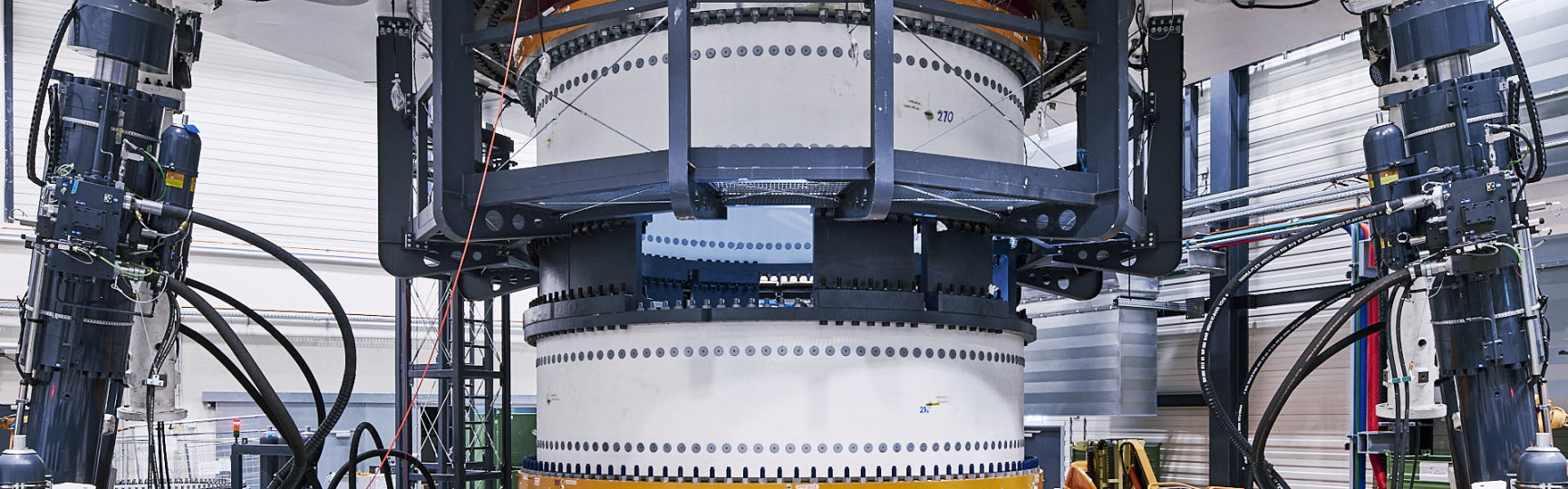
Stochastische Lasten, variierenden Drehzahlen, Schnittstellen mit komplexen Steifigkeitsprofilen: Die Lebensdauer von Wälzlagern in Windenergieanlagen (WEA) hängt von zahlreichen Einflüssen ab. Mit dem Large Bearing Laboratory (LBL) verfügt das Fraunhofer IWES über eine einzigartige Methodenkompetenz sowie Prüf- und Forschungsinfrastruktur zur Zuverlässigkeitssteigerung der Lager. Zur Absicherung von Produkteigenschaften mechanischer WEA-Antriebsstränge entwickelt und realisiert das IWES Validierungsstrategien, Prüfkonzepte, Prüfstände, Messmethoden, Prüfkampagnen, CAE-Modelle uvm. Für die Statiksicherung der Turbine müssen bei den WEA-Tragstrukturen – z. B. Turm, Fundamente und notwendige Anbauteile – Design und Fertigung entsprechend der wachsenden Betriebslasten optimiert werden. Das IWES entwickelt Angebote zur Reduzierung der wirtschaftlichen und technischen Risiken künftiger Tragstrukturen.
Für großmaßstäbliche WEA-Gondelprüfungen verfügt das IWES mit dem Dynamic Nacelle Laboratory (DyNaLab) über einen weltweit einzigartigen Prüfstand. Er enthält ein leistungsstarkes Lasteinleitungssystem (LAS), das als Hexapod mit einem großen Momentenlager ausgestattet ist, und bietet für aussagefähige Labortests ein realitätsnahes Testumfeld im Multimegawattbereich.
Ausfälle von WEA-Triebsträngen zählen zu den Hauptursachen von Stillstandszeiten. Virtuelle Tests mittels Simulationsmodell und validierter Messdaten lassen bereits im Entwicklungsprozess Belastungen erkennen. In der Erhebung und Verarbeitung entsprechender Messdaten bietet das IWES außergewöhnliche Erfahrung.
Die Tragstrukturen einer Windenergieanlage (WEA) umfassen alle Komponenten, die die Statik der Turbine sicherstellen: Turm, Fundamente und notwendige Anbauteile, den sogenannten Secondary Steel. Sowohl onshore als auch offshore steigen dabei die Nennleistungen der Anlagen kontinuierlich weiter und damit auch die Betriebslasten, die über die Tragstrukturen aufgenommen werden müssen. Die Bausteine, aus denen diese zusammengesetzt sind, gehören mittlerweile zu den größten Stahlbauteilen überhaupt. Hersteller und Designer sehen sich dabei mit einer Reihe von Herausforderungen konfrontiert: Beispielsweise müssen schwingfeste Schweißverbindungen mit sehr hoher Wandstärke (> 100 mm) sicher hergestellt und das Verhalten des Baugrunds über die Lebensdauer einer Anlage von mindestens 25 Jahren vorausgesagt werden. Das IWES entwickelt hierfür viele Angebote, die das wirtschaftliche und technische Risiko von Tragstrukturen der nächsten und übernächsten Generation entscheidend senken können.
Mit den steigenden Nennleistungen von Windenergieanlagen nehmen auch die Anforderungen an deren Tragstrukturen kontinuierlich zu. Hersteller sind gefordert, für die wachsenden Betriebslasten Design und Fertigung der notwendigen Bauteile anzupassen. Das IWES entwickelt zu diesem Zweck zahlreiche Angebote, die wirtschaftliche und technische Risiken von künftigen Tragstrukturen signifikant verringern können.
Im Fokus dabei stehen ein fertigungs- wie anwendungsgerechtes Design, z. B. Untersuchungen des spezifischen Tragverhaltens von Saugeimergründungen - sogenannte Suction Caissons - sowie die Entwicklung und Validierung von Materialmodellen, mit deren Hilfe sich der Baugrund in der Nordsee modellieren lässt. Design und Fertigung einer Tragstruktur für eine Windenergieanlage sind aufgrund der enormen Dimensionen dieser Bauteile immer eine Herausforderung. Wir unterstützen Kunden bei den Installationen on- und offshore, ober- und unterhalb der Erdoberfläche.
Die Wandstärken von Türmen und Pfahlgründungen betragen bei aktuellen Anlagentypen teilweise mehr als 100 mm. Die betriebsfeste Auslegung von Schweißnähten ist komplex – die üblicherweise herangezogenen Wöhler-Kennlinien existieren für diese Dimensionen kaum, und auch in der Prozesstechnik sind diese Abmessungen unter den Lastfällen einer Windenergieanlage heraufordernd.
Wir unterstützen bei der Qualifizierung und Optimierung von Schweißnahtformen hinsichtlich Ermüdung, beispielsweise auf Basis von optischen Methoden zur Bestimmung der Mikro- und Makrogeometrien. Unsere validierten numerischen Modelle unterstützen beim fertigungs- und anwendungsgerechten Design sowie bei der Senkung von Kosten und Technologierisiken.
Suction Caissons oder Saugeimergründungen sind eine umweltschonende und effiziente Methode, eine Offshore-Windenergieanlage zu gründen. In der Anwendung zeigen sich jedoch immer wieder Hindernisse bei der Installation, die es zu überwinden gilt: Die Strukturen können teilweise nicht auf die geplante Tiefe eingebaut werden und sind bei einer Überlastung während des Einsaugens anfällig gegenüber einem Beulversagen. Das IWES entwickelt hierfür experimentell validierte numerische Modelle, um das komplexe Verhalten des Suction Caissons während des Einbaus zu modellieren und somit den Windparkplanern ein Werkzeug zur Verfügung zu stellen, das den Installationsprozess insgesamt verlässlicher machen kann.
Ein weiterer Schwerpunkt unserer Aktivitäten ist die Untersuchung des spezifischen Tragverhaltens von Suction Caissons in geotechnischer Hinsicht, das insbesondere im dynamischen Lastbereich noch Potential zur Massen- und Kostenoptimierung bieten kann.
Der Baugrund in der Nordsee ist überwiegend wassergesättigter Sand mit je nach Region unterschiedlichen Lagerungsdichten. Dieser Baugrund bietet die Möglichkeit, verlässliche Gründungen (Fundamente) zu realisieren, ist aber gleichzeitig ein hochkomplexer Werkstoff mit stark nichtlinearem Verhalten. Die Vorhersage der für die Planung einer WEA notwendigen mechanischen Eigenschaften des Bodens – insbesondere über die gesamte Lebensdauer einer Anlage gesehen – ist kontinuierlich Gegenstand von intensiven Forschungen. Das IWES entwickelt und validiert hierfür komplexe numerische und analytische Materialmodelle, mit der sich sowohl die für das Design wichtige Bettungssteifigkeit des Baugrunds als auch die Veränderung des Bodens über die Laufzeit des Betriebs bewerten lassen. Besonders wichtig ist hierbei die Berücksichtigung der Effekte des Einbaus der Gründung selbst: Die Installation z. B. einer Pfahlgründung über Impact- oder Vibrationsramme verändert den Baugrund um den Einbauort herum und muss bei der Bemessung des Fundaments berücksichtigt werden. Analyse und Bewertung von Installationseinflüssen stellen einen Arbeitsschwerpunkt des IWES dar.
Testzentrum Tragstrukturen am Fraunhofer IWES
Wälzlager erreichen in den meisten industriellen Anwendungen eine sehr hohe Lebensdauer. Die Einsatzbedingungen für und die Anforderungen an die Wälzlager von Windenergieanlagen unterscheiden sich jedoch maßgeblich von Standardanwendungen: Hohe stochastische Lasten, oszillierende Schwenkbewegungen, ständig variierende Drehzahlen und Schnittstellen mit komplexen Steifigkeitsprofilen erschweren die Auslegung und können dazu führen, dass Ausfälle weit vor Ende der berechneten Lebensdauer nicht ungewöhnlich sind.
Insbesondere im Bereich der Rotorblattlager betreibt das Team des Fraunhofer IWES mit dem „Large Bearing Laboratory“ (LBL) eine einzigartige Forschungsinfrastruktur und hat entsprechende Methodenkompetenz aufgebaut. Von validierten Berechnungsmethoden, der Ausfallursachenanalyse bis zu skalierten, realmaßstäblichen und dabei stets anwendungsnahen Prüfungen bietet das LBL alles an, um die Windenergiebranche bei Auslegung, Betrieb und Eigenschaftsvalidierung im Bereich dieser anspruchsvollen Komponenten zu unterstützen.
Für oszillierende Wälzlager, wie sie im Bereich der Rotorblattlagerung eingesetzt werden, existieren nur bedingt aussagekräftige Methoden zur Berechnung der Lebensdauer.
Stillstandsmarken, Ringbrüche, Kontaktkorrosion, Kernversagen und Verschleiß sind typische Beispiele für auftretende Schäden, die zu vorzeitigen Ausfällen und somit zu hohen Kosten und Sicherheitsrisiken führen können. Die Einbausituation, die Belastungen, die spezifischen Betriebsbedingungen, das eingesetzte Schmiermittel und vieles mehr haben einen Einfluss auf die Zuverlässigkeit dieser großen, aber sensiblen Komponenten. Durch stetig wachsende Anlagen und kurze Markteinführungszeiten steigen zusätzlich nicht nur die Anforderungen, sondern auch das Risiko. Das Fraunhofer IWES forscht daher seit 2013 an den Großwälzlagern von Windenergieanlagen (WEA), um ihre Zuverlässigkeit zu steigern sowie neuen Berechnungsmethoden und Designs den Weg zu ebnen. Das LBL am Institutsstandort Hamburg bündelt diese Aktivitäten und erweitert sie um experimentelle Testmöglichkeiten für Lager von WEA der nächsten Generation.
Mit dem LBL betreibt das IWES in Hamburg eine einzigartige Prüfinfrastruktur, die die Untersuchung grundlegender Einflussfaktoren der vielfältigen Schadensbilder sowie die realmaßstäbliche Validierung großer Drehverbindungen ermöglicht. Durch die enge Vernetzung mit weiteren Institutsteilen, kann auf die Prüfinfrastruktur des gesamten Institutes zurückgegriffen werden, um auf Anforderungen verschiedenster Lagerstellen zu reagieren. Die Prüfstrategie des LBL ist prinzipiell unterteilt in eine Funktions- und eine Dauerprüfung. Während der Funktionsprüfung werden dominierende Schadensmechanismen im Lager bestimmt. Diese Schadensmechanismen bestimmen das Programm der anschließenden gerafften Lebensdauerprüfung. Die Aufstellung des Testprogramms, ausgehend von den Zeitreihen der Lastsimulation, wird ebenfalls im LBL durchgeführt. Eine umfangreiche Datenanalyse erlaubt dabei die Beschleunigung bzw. Raffung der Testdauer auf Laufzeiten, die innerhalb der Entwicklung einer WEA vertretbar sind. Die begleitende Simulation der Lager unterstützt die Prüftätigkeiten und umfasst Einzelkontaktsimulationen sowie globale Lagermodelle für FE- und MKS-Analysen. Die Schnittstellen (Rotorblatt, Verschraubungen, Rotornabe, Lagergehäuse, Lagersitz, etc.) werden ebenfalls in FE-Modellen abgebildet. Alle Simulationsmodelle werden mit Messdaten abgeglichen und validiert. Von der Konzeptentwicklung über die Simulation, Auslegung, Prüfung und schließlich Begutachtung deckt das IWES LBL-Portfolio somit den kompletten Lebenszyklus eines Großwälzlagers ab.
So individuell wie jedes Lager sind auch die Anforderungen und Herausforderungen. Aufgrund der langjährigen Erfahrung aus über 300 getesteten Lagern und dem Betrieb sowie der Entwicklung von mehr als acht Prüfständen verfügt das Team des LBL über einen großen Erfahrungs- und Wissensschatz. Die stetige Weiterentwicklung unserer Methoden und den Fokus auf eine anwendungsnahe Forschung bringen wir in jedes Projekt mit ein. Zusammen mit den Kunden werden die individuellen und spezifischen Anforderungen identifiziert und maßgeschneiderte Lösungen entwickelt, um eine optimale Validierung des gesamten Blattverstellsystems zu gewährleisten.
Lagerprüfstand BEAT6.1 des Fraunhofer IWES
Wettbewerbsdruck und zunehmende Professionalisierung der Branche erhöhen die Anforderungen an WEA-Gondeln. WEA mit neuem Design müssen bereits von Anfang an zuverlässig laufen.
Vor der Finanzierungszusage verlangen Investoren den Nachweis umfangreicher Betriebserfahrung. Für Hersteller bedeuten Modifikationen wie Neuentwicklungen erhebliche wirtschaftliche Risiken. Eine experimentelle Validierung von Prototypen auf Großprüfständen verringert diese Risiken, beschleunigt die Zertifizierung und sorgt für bessere Planbarkeit.
Der höhere Stromanteil regenerativer Quellen in den Verteil- und Übertragungsnetzstrukturen lässt die Anforderungen an die Netzintegration von WEA weiter steigen. Normen und Richtlinien müssen diese Entwicklung berücksichtigen. Zwingend erforderliche Anlagenzertifikate für Neu- und Weiterentwicklungen gewährleisten einen netzkonformen Betrieb und garantieren den dauerhaften Netzanschluss und Erhalt von Einspeisevergütungen.
Mit effizienten Testmethoden unterstützt das IWES Anlagenhersteller dabei, steigenden Anforderungen gerecht zu werden.
Die Prüfung der Netzverträglichkeit zur Zertifizierung elektrischer Eigenschaften neuer Windenergieanlagen (WEA) oder zur Nachzertifizierung bei Änderungen bestehender Anlagentypen erfolgt oft mit Hilfe mobiler Prüfeinrichtungen im Feld. Die Zertifizierungskampagne dauert meist bis zu zwei Jahre, ist ein wesentlicher Kostenfaktor der Anlagenentwicklung und verzögert den Zeitpunkt der Markteinführung.
Die Nachfrage nach geeigneten Standorten zur Prototypenzertifizierung ist groß, ebenso die Anzahl der zu zertifizierenden Anlagen. Zu berücksichtigen sind ein gutes Windangebot sowie – durch zunehmende Anlagengröße – erhöhte Anforderungen für den Netzanschluss. Feldversuche sind nicht reproduzierbar und Ergebnisse nur beschränkt vergleichbar, da Wind- und Netzverhältnissen nie identisch sind. Wartezeiten erschweren die Planung der Markteinführung zusätzlich.
Das Dynamic Nacelle Testing Laboratory (DyNaLab) bietet seit 2015 ein realitätsnahes Testumfeld im Multimegawattbereich für aussagefähige Labortests. Mit einer Antriebsleistung von 10 MW und der Einleitung eines nominellen Drehmoments von 8,6 MNm werden einmalige Prüfleistungen zur Prototypenvalidierung angeboten. Durch die Netz- sowie HiL-Windlastsimulationen können unterschiedliche Belastungsszenarien unter reproduzierbaren Bedingungen erstellt werden. Getestet wird zudem das Verhalten einer WEA bei Szenarien wie Multidips im Netz bei Sturm, Netzkurzschluss bei fehlerhafter Pitchregelung oder Notstopps.
Durch die Reproduzierbarkeit unterschiedlicher Betriebsfälle lassen sich die Zertifizierungskampagnen stark verkürzen. Betriebsführung und Regelung können optimiert und Modellvalidierungen durchgeführt werden. Dies steigert die Zuverlässigkeit und Verfügbarkeit der Anlage und senkt, Wartungs- und Reparaturkosten.
Das DyNaLab bietet realitätsnahe Prüfbedingungen im Multimegawattbereich. Bestehende und künftige WEA-Konzepte können so validiert und optimiert werden. Durch den Einsatz eines virtuellen Netzes mit 44 MVA installierter Umrichterleistung lassen sich typische Netzfehler wie Spannungseinbrüche mit hoher Wiederholfrequenz nachbilden.
Die Kombination aus mechanischen Tests mit einem Netzemulator zur Prüfung von WEA bis 10 MW ist in dieser Konfiguration weltweit einzigartig. Der Prototyp der AD 8-180 wurde ebenso getestet wie ein supraleitender Generator des Forschungsprojektes EcoSwing, und auch Enercon, GE und Siemens Gamesa Renewable Energy (SGRE) haben den Gondelprüfstand für Testkampagnen genutzt.
Durch statische Tests lässt sich auch die Wirk- und Blindleistungsabgabe bei unterschiedlichen Netzzuständen ermitteln. Zudem können transiente Netzereignisse simuliert werden, die sich auf das Gesamtsystem Gondel auswirken: Tests von dynamischen Low-Voltage-Ride-Through (LVRT)- und High-Voltage-Ride-Through (HVRT)-Ereignissen, wie sie von unterschiedlichen Grid Codes gefordert werden, sowie dynamische Änderungen der Netzfrequenz.
Da die Gondel im Prüfstand ohne Rotor und Turm getestet wird, weist sie andere Systemeigenschaften als im Feld auf. Zur Nachbildung der realen Bedingungen werden die auftretenden Lasten und Wechselwirkungen zwischen Gondel und Rotor berechnet und im Prüfstand auf die Gondel eingeprägt. Leistungsfähige Echtzeitmodelle und Regelungsalgorithmen sorgen dafür, den Prüfstand inklusive Prüfling im Hardware-in-the-Loop-Verfahren (HiL) zu betreiben. Zertifizierungsprüfkampagnen lassen sich somit genau terminieren und herstellerspezifisch definieren.
Das Fraunhofer IWES unterstützt dabei, die auf dem Prüfstand erlangten Ergebnisse mit Feldmessungen abzugleichen. Mittels enger Zusammenarbeit mit dem Anwendungszentrum Feldmessungen im Bereich Messtechnik und Sensorik werden Synergien erschlossen. Die enge interne Verknüpfung von Feldmessungen und Testbetrieb bietet die Möglichkeit, akkreditierte Lastmessung gemäß IEC 61400-13 durchzuführen.
Supraleitender Generator auf dem Prüfstand
Triebstränge von Windenergieanlagen (WEA) sind im Betrieb komplexen dynamischen Belastungen ausgesetzt. Ihre Ausfälle zählen zu den Hauptursachen von Stillstandszeiten. Moderne Simulationswerkzeuge wie flexible Mehrkörpersimulation (MKS), die finite Elemente Methode (FEM) sowie die Integration multiphysikalischer Modelle erhöhen das Systemverständnis. Auslegungsprozesse können so verbessert, die Zuverlässigkeit des Triebstrangs erhöht werden.
Virtuelle Tests mittels Simulationsmodell lassen bereits im Entwicklungsprozess Belastungen erkennen. Kostenintensive physikalische Prüfungen lassen sich so erweitern und bspw. durch Parametervariationen ergänzen.
Zur Sicherstellung der Gültigkeit der verwendeten Modelle ist eine Validierung mit Messdaten wichtig. Das Fraunhofer IWES greift dazu auf jahrelange Erfahrung in der Erhebung und Verarbeitung entsprechender Messdaten zu. Validierte Simulationsmodelle erlauben verlässliche Aussagen über bestehende und neue Triebstrangkonzepte.
Zur Validierung neuer Triebstrangdesigns und -technologien sind auch die größten Systemprüfstände kaum noch ausreichend leistungsstark.
Um diesem Problem zu begegnen, haben wir am Fraunhofer IWES das Verfahren des hybriden Testens entwickelt und zum Patent angemeldet. Es kombiniert physikalische Prüfungen mit modernen Simulationsmethoden, um eine hybride Prüfung von Triebsträngen auch oberhalb der Maximallast des Prüfstands zu ermöglichen.
Zur Erhöhung der Zuverlässigkeit von WEA-Triebsträngen ist ein genaues Verständnis der wirkenden dynamischen Belastungen und Betriebszustände erforderlich. Unsere Simulationswerkzeuge und -modelle helfen dabei – so kann bspw. der Einfluss von Gleitlagerungen im Getriebe auf die Systemdynamik des gesamten Triebstrangs näher untersucht und quantifiziert werden. Die virtuellen Prüfungen unterstützen beim Auslegungs- und Entwicklungsprozess der Stränge und Komponenten und ermöglichen u. a. eine höhere Zuverlässigkeit und Drehmomentdichte sowie mehr Leichtbauweisen. Zudem werden etwaige Vibrationen und Resonanzstellen aufgezeigt, die zu schädigungsrelevanten Belastungen des Triebstrangs führen können. Physikalische Prüfungen auf einem Komponenten- oder Systemprüfstand, begleitet von virtuellen Tests, erlauben Parametervariationen sowie die effiziente Erweiterung der Prüfergebnisse.
Mit unseren Simulationsmodellen bieten wir unseren Kunden bessere Prüfmethoden und einzelne Prüfsequenzen. Auch nachgelagerte Fragestellungen werden beantwortet – etwa für die Entwicklung von Condition-Monitoring-Systemen oder die Optimierung der Anlagenregelung. Die Modelle unterstützen zudem bei realen Prüfkampagnen, etwa auf dem Gondelprüfstand oder auf einem der Komponentenprüfstände. Zudem lassen sich vorab konkrete Prüfszenarien erproben und optimieren. Während der Prüfkampagne helfen unsere Simulationsmodelle, die Messergebnisse zu verifizieren und unerwartete Daten oder Phänomene besser zu verstehen
Hierfür kann der Großteil der vorgesehenen Prüfungen unterhalb der Maximalkapazität des Prüfstands physikalisch auf dem realen Prüfstand erfolgen. Mittels gewonnener Messdaten wird ein Simulationsmodell des Prüflings in Teillast validiert und optimiert. Mit diesem Modell werden anschließend virtuell jene Prüfungen durchgeführt, die die physikalische Prüfstandskapazität überschreiten. Die Kombination der physikalischen Messergebnisse mit den Simulationsergebnissen bis zur Maximalbelastung des Prüflings ergeben eine realistische Nachbildung eines vollständig physikalischen Triebstrangtests. Durch die Nutzung kleinerer und erprobte Prüfstände werden Investitions- und Prüfkosten eingespart.
Grundlage unserer Triebstrangsimulationen sind detaillierte Simulationsmodelle, häufig auf Basis flexibler Mehrkörpersimulation oder der Finite-Elemente-Methode (FEM). Zu unseren Kernkompetenzen zählen die Entwicklung und Implementierung von Simulationsmodellen zur Vorhersage von Systemeigenschaften des WEA-Triebstrangs und seiner Komponenten. Zur Optimierung der Modellgenauigkeit ist die Validierung mittels realer Messdaten der entscheidende Schritt. Er beinhaltet sowohl den Vergleich mit physikalischen Daten als auch die darauf basierende Anpassung und Optimierung des Simulationsmodells.
Wir unterstützen bei zielgerichteten, effizient durchgeführten Modellvalidierungen, beraten bei der Planung von Prüfungen zur Modellvalidierung und empfehlen u. a. geeignete Prüfszenarien und den Einsatz spezieller Sensoren. Zudem helfen wir auf Basis der Messergebnisse, konkrete Modellparameter zu identifizieren und anzupassen.
Die experimentelle Untersuchung und Validierung vorhandener oder in der Entwicklung befindlicher Komponenten und Untersysteme des mechanischen Antriebsstrangs von Windenergieanlagen stellt den wesentlichen Entwicklungsschritt hin zur Absicherung der geforderten Produkteigenschaften dar. Neben der Risikominimierung und der damit verbundenen Vertrauensbildung in das Produkt ermöglicht die durch das Experiment gestützte Validierung die Chance, in der Entwicklung genutzte (Auslegungs-)Modelle zu validieren und somit bspw. existierende Bauteilreserven auszuschöpfen.