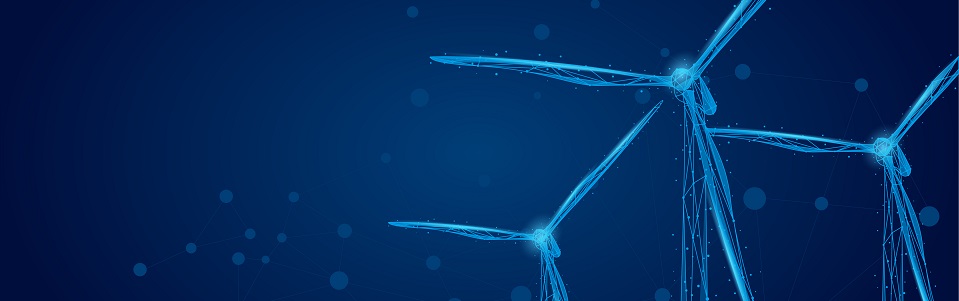
The project partners are investigating the linking of lightweight construction principles and the digitalized production of offshore wind turbines with the aim of saving resources and reducing CO2 emissions. BMWK, 05/2021 - 04/2026
more infoDigitalization is a dynamic and clearly noticeable process in industry – including the wind energy and hydrogen sectors. Through its complex research topics, Fraunhofer IWES offers digital solutions in all areas. In addition to standards such as data monitoring, topics such as big data and the digital twin have also found their way into research. They are being utilized and further developed in a wide range of different scientific fields.
Virtual test rigs are a major focus at Fraunhofer IWES among other things. The physical test rigs are used to develop numerical models and validate them fully with experimental tests. This enables the development of new test methods which are not physical.
At the Dynamic Nacelle Testing Laboratory (DyNaLab), for example, it is possible to describe a mechanical test. The model represents a nacelle, the surrounding test infrastructure, and the auxiliary systems. The virtual nacelle test rig can also map the effects of electrical tests on the mechanical structure.
In addition to a range of software used in-house, IWES also makes open source fluid dynamics software available to external users. FOXES, a modular wind farm simulation and wake modeling toolbox, and iwopy, a framework for coupling different optimization modules, together form the basis for calculating different optimization scenarios of wind energy utilization.
Use cases range from wind farm optimization (e.g., layout optimization or wake steering) to post-construction analyses, studies, comparisons, and wake model validations. Further open source releases are also planned for the future.
The project partners are investigating the linking of lightweight construction principles and the digitalized production of offshore wind turbines with the aim of saving resources and reducing CO2 emissions. BMWK, 05/2021 - 04/2026
more infoThe project partners are improving methods for the calculation of vortex-induced vibrations so as to be able to include these phenomena in the early phase of rotor blade design. BMWK, 07/2023 – 12/2025
more infoThe project partners are investigating new mathematical methods of flow simulation in order to make them applicable for use in wind energy with lower computing efforts and higher accuracy. BMWK, 07/2022 - 06/2026
more infoThe project partners are developing a toolbox for direct stability assessment during real-time operation of large power grids with 100 percent renewable energy. BMWK, as part of the EU initiative Clean Energy Transition Partnership (CETP), 12/2024 - 11/2027
more infoThe international project partners are developing a customizable digital twin for offshore wind farms. Horizon Europe, 06/2024 – 05/2027
more infoThe project partners are employing a digital twin of a real offshore wind farm to develop a strategy for flexible control. BMWK, 11/2022 - 10/2025
more infoThe project partners are working to derive new wind field models that will improve the design of large and high wind turbines and enable the revision of the current standard. BMWK, 02/2021 – 01/2025
more infoThe project partners are developing an AI-supported diagnostics system for verifying power curves and detecting faults for a higher energy yield from wind. BMBF, funding program KI4KMU, 04/2024 - 03/2026
more infoThe project partners are improving and validating calculation and simulation methods for the testing and design of rotor blades. BMWK, 05/2021 - 04/2025
more infoThe project partners are developing a method for the creation of digital twins of large rolling bearings in order to improve their condition monitoring and reliability. BMWK, 07/2022 - 12/2025
more info