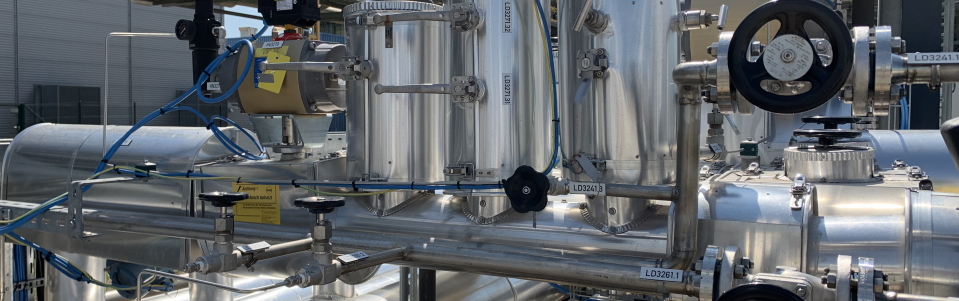
The project partners are developing a one-stop-shop to permit cross-industry and cross-sector knowledge and technology transfer for structural change in the Central German mining region. BMWK, 01/2023 – 12/2026
more infoThe production of green hydrogen for the decarbonization and defossilization of industrial processes will make a decisive contribution to the achievement of the climate goals. The reliable operation of electrolyzers and systems all along the H2 value chain is key to minimizing the risks of upscaling hydrogen production.
The rapid ramp-up and the associated immense increase in demand for electrolysis capacity pose challenges not only for manufacturers but also for future operators, as not only production processes, but also measurement and monitoring procedures are not easy to scale up from the factory to industrial dimensions.
Embedding in the energy system and in industrial processes also poses challenges in terms of deployment behavior and operating models. This is why Fraunhofer IWES operates three hydrogen labs for the testing and validation of hydrogen-relevant components along the value chain: from production via electrolysis to storage and use in PtX processes or fuel cells – with a total connected power of more than 25 MW. In doing so, Fraunhofer IWES is helping the industry to establish a sustainable hydrogen economy. The hydrogen labs have different focuses:
The offer ranges from stack testing in the 45 kW range up to multi-megawatt testing capacity for operation under real conditions. Dynamic loads are simulated, as are environmental conditions and mechanical loads. Digital simulations accompany the process, describe procedures, and serve to optimize techno-economic key figures. Analyses are carried out across the board in order to develop methods and test procedures for electrolyzer materials and components and to apply them on a laboratory scale. The services offered include real-time monitoring of H2 and O2 purity, GC-MS trace analysis of material flows, electrochemical evaluation of components, and fault diagnostics.
IWES can draw on many years of expertise in standardization issues in the wind industry. The partnerships with and expertise of pioneering institutions and companies enable IWES to develop standardized test procedures for hydrogen technologies.
The project partners are developing a one-stop-shop to permit cross-industry and cross-sector knowledge and technology transfer for structural change in the Central German mining region. BMWK, 01/2023 – 12/2026
more infoIn the ONTOHY project, the project partners (Fraunhofer IWES and IWU) are creating a digital data and knowledge collection for the topic of hydrogen with the aim of supporting the structural change in the region of Lusatia in Eastern Germany. BMWK, BAFA, 04/2021-12/2026
more infoThe best conditions for generating renewable wind energy can be found at sea. The direct production of green hydrogen from wind energy in offshore turbines without a grid connection can lower the costs considerably compared with onshore generation. The H2Mare flagship project will thus investigate the offshore generation of green hydrogen and other power-to-X products. BMFTR, 04/2021-12/2025
more infoThe project partners are developing an innovative electrolysis system with storage technology which is optimally adapted to the offshore environment for deployment at sea. BMBF, 04/2021 - 12/2025
more infoCost-efficient huge capacities electrolyzers are required to satisfy Germany’s green hydrogen demand. Although there are already high-performance electrolyzers available on the market today, they are still largely built by hand. The H2Giga flagship project will therefore support the serial production of electrolyzers. BMBF, 04/2021 - 12/2025
more infoThe project partners are developing monitoring and diagnostic tools, which will be combined with an electrolyzer management system permitting more efficient operation, a longer lifetime, and increased reliability of the systems, even on an industrial scale. Clean Hydrogen Partnership, co-funded by the European Union, 01/2025-12/2027
more infoThe project partners are developing a coupled process chain of innovative individual technologies for the cost-efficient and scalable production of e-methanol. BMDV (NOW) and coordinated by VDI/VDE, 08/2023 - 07/2026
more infoThe project partners are developing concepts for an innovative design and the optimal operation of offshore wind turbines and electrolyzers for the production of green hydrogen with simultaneous reduction of the use of rare earth elements. BMBF in the scope of SBEP, 05/2024 – 04/2027
more infoThe project partners in the ViR technology network are developing the digital twin of a fuel cell factory as part of the H2GO project. BMDV, 05/2022 - 11/2025
more infoThe goal of the Northern German Regulatory Sandbox (Norddeutsches Reallabor NRL) is to test the transformation path for an integrated energy system that will succeed in reducing CO2 emissions in the North by 75 percent by 2035. BMWK, 04/2021–03/2027
more info