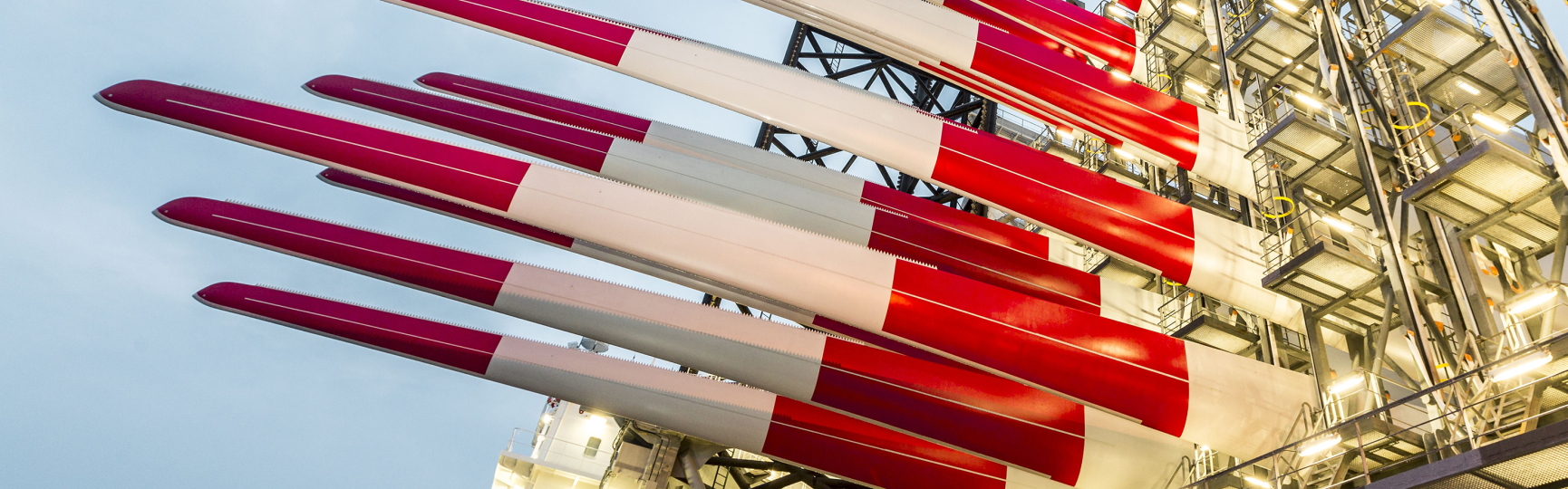
The rotor blades of large offshore wind turbines have now surpassed the 100-meter mark and continue to increase in size. This growth is pushing the structural load-bearing capabilities to their limits, rendering a thorough understanding of the complex mechanical behavior of composite materials under fatigue loading indispensable. At the same time, the reliable and efficient production of wind turbine blades of this scale is a task which demands advances in production techniques and in automation. With its unique research infrastructure, Fraunhofer IWES is in a position to support the wind industry across scales and in all technical domains. IWES is your one-stop shop for everything you need for the research and development of wind turbine blades: from full-scale testing of the rotor blades to micro-CT scans of fiber orientation, from innovative production technologies to the recycling of end-of-lifetime (EoL) blades and much more.
Research rotor blade production at Fraunhofer IWES
Intensive validation across scales is necessary to ensure the reliable operation of wind turbine blades for 20, 25, or even 40 years. IWES operates an IECRE-recognized laboratory for the testing of wind turbine blades with three test benches for certification tests according to IEC 61400-23. The largest test bench can achieve a maximum fatigue bending moment amplitude of 140 MNm.
With a track record of more than 40 completed full-scale blade test campaigns, IWES is known throughout the industry for its high levels of reliability and flexibility as well as its ability to react. Among the leading research institutes, IWES is a pioneer in the employment of innovative approaches for the testing of rotor blades. Dual-axis testing in a 1:1 elliptical excitation is available for commercial tests, and the same applies for the sequential approach to segmented testing.
Modular test benches which can accommodate a large range of tip segment and 1:1 subcomponent tests complete the service portfolio. To develop new test methods, IWES relies on a proprietary software tool for the optimization of test setups, and also offers this tool to customers.
The accurate prediction of the fatigue behavior of composite materials requires a deep understanding of both the materials themselves and also the manufacturing processes. IWES operates a material lab. Standard material tests are, of course, available, but our real strength shines through when developing new test setups for special requirements. Systems are tested for rain erosion and ice accretion in the Leading Edge Lab.
IWES is the only institute capable of manufacturing specimens from coupon size to full wind turbine blades. This helps with the testing of the manufacturability of novel materials and ensures a seamless market introduction. At the same time, processing large-scale components enables us to validate manufacturing-centered material models, such as advanced curing kinetics models.
Automated production processes are always a case-by-case decision for wind turbine blades. Achieving the optimal balance between investment costs, production rate, flexibility of production, operational costs, and the in-field reliability of the blade is particularly important.
IWES provides support in the search for optimal solutions for manufacturing challenges. To do so, we combine and integrate existing commercial products, taking customized, customer-specific technological developments into consideration. The BladeMaker demonstration center is an ideal development environment for both us and our customers.
In addition, IWES also works independently on process developments such as the variable paste shoe, which has been patented and is available through license agreements with our partners. With our approach to direct molding for prototype molds, we have demonstrated a means of significantly reducing lead times.