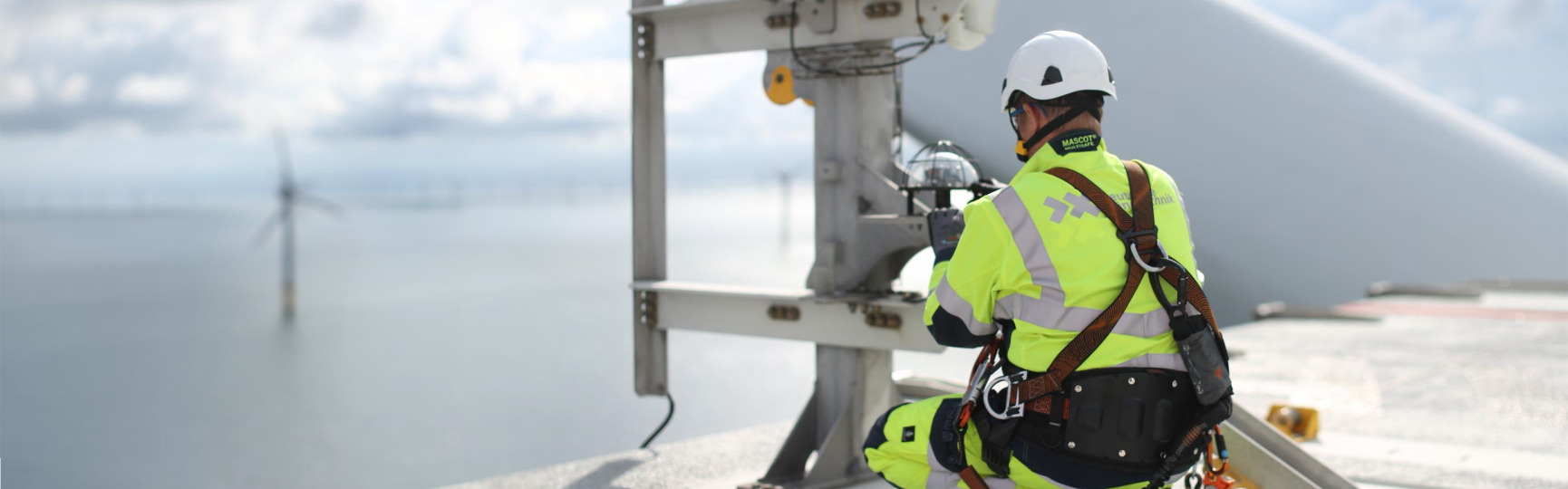
Reliable statements on the efficiency, functionality, and service life of wind turbines are essential for their realization. To this end, IWES performs measurements on turbines in operation, tests mechanical loads and determines their performance behavior at the Application Center for Wind Energy Field Measurements (AWF). To research the aero-servo-hydro-elastic simulation of wind turbines, IWES programs the MoWiT simulation model for load calculation and real-time simulation. MoWiT is used to optimize wind energy systems and develop AI models. IWES is also promoting the development of sustainable shipping. In cooperation with the Emden/Leer University of Applied Sciences, the focus is on wind propulsion systems, design concepts, and emission reduction.
The dynamically increasing competition in the wind energy sector demands high-quality, efficient processes with which prototypes and old turbines in the field can be measured, analyzed, and optimized. As with banks and insurance companies, developers, manufacturers, operators, and technical service providers require reliable information about the efficiency, functionality, and service life prospects of their turbines.
The Application Center for Wind Energy Field Measurements (AWF), a cooperation between Fraunhofer IWES and fk-wind at Bremerhaven University of Applied Sciences, offers (as a partner in R&D projects) the measurement of turbines in operation as a service.
AWF boasts highly qualified (scientific and technical) staff and is an accredited testing and calibration laboratory in accordance with ISO 17025 for the measurement of mechanical loads and the assessment of the power performance characteristics of wind turbines. In addition, it also has the unique testing infrastructure of the entire IWES at its disposal.
AWF at IWES plans and conducts measurements of wind turbines, applying the relevant national and international standards and guidelines in consultation with the customer. The data recorded include meteorological variables and the power performance in accordance with IEC 61400-12 and/or load parameters in accordance with IEC 61400-13.
In addition to standard-specific measurements of the full wind turbine, measurements are also conducted on specific components of wind turbines (e.g., bearings, rotor blades, etc.) in particular. When doing so, the full expertise of the other IWES departments in these components gathered on the institute’s own test benches can be incorporated into the planning, conduction, and evaluation of the measuring campaigns.
In addition, the most important operating data of the wind turbine, such as the azimuth position and speed, are also recorded for the evaluation and interpretation of the measurement data. Furthermore, AWF also offers to conduct special measuring campaigns (e.g., in acc. with VDI 3834) and other customer-specific measurements on all turbine components. This includes, among other things, the measurement of the aeroelastic behavior of rotor blades, a field in which extensive experience has been gained in recent years. In the field of acoustics, AWF offers both measurements of the acoustic noise in accordance with IEC 61400-11 and measurements with the acoustic camera to locate sound sources.
View from above: Implementation of standardized and customer-specific measurement projects on wind turbines © Fraunhofer IWES
The Global Systems Dynamics group at Fraunhofer IWES conducts research in the field of aero-servo-hydro-elastic simulations of wind turbines with a focus on improving simulation and validation methods for onshore, offshore, and floating wind turbines. The MoWiT simulation model for load calculations and real-time simulation was programmed specifically for this purpose. MoWiT forms the basis for the optimization of wind energy systems using a proprietary Python-based optimization and automation framework as well as for the development of AI models.
Questions such as the capacity of floating wind turbines to self-align and the resulting effect on the energy yield are answered utilizing customer-specific simulation studies, and new methods are employed to verify the validity of current simulation models.
Fraunhofer IWES conducts research in the field of floating wind turbines and offers services from the modeling to the validation of numerical simulation models. This encompasses the validation of manufacturer specifications on the dynamics of the floating system model via numerical simulation studies and the comparison with measurement data from tank tests. It also includes simulative analyses of the self-alignment capacity when using a single-point mooring and the resulting effect on the annual energy yield.
The spectrum of services also comprises the scaling of floating wind energy systems for future turbine sizes. This allows the determination of mechanical loads for various foundation concepts and makes it possible to assess the costs for future, floating wind farms.
For future issues relating to the performance of system services, models of the power electronics and the mechanical drive train are coupled in a holistic approach and their interaction in the event of grid faults as well as the resulting effect on the dynamics of the floating wind turbine are analyzed.
The floating system model in MoWiT is real-time capable and thus suitable for integration in popular real-time hardware (e.g., Opal-RT, Beckhoff) for Hardware-in-the-Loop applications. Among other uses, MoWiT is employed at the IWES test benches DyNaLab and HiL-GridCoP as a real-time model for Hardware-in-the-Loop simulation as a digital twin of customer wind turbines.
Component tests have an ever greater role to play for future turbine sizes, with the relevance of validated component models increasing as a result. IWES offers validation methods that allow assessment of the validity of existing simulation models and thus help the customer to reduce risks in the modeling.
IEA Task 30 OC4 Phase II floating semi-submersible offshore wind turbine in MoWiT © Fraunhofer IWES
The Fraunhofer Working Group Sustainable Maritime Mobility (SMM) at IWES is boosting research and development for sustainable shipping. Under the joint leadership of Hans Kyling from Fraunhofer IWES and Professors Jann Strybny and Michael Vahs from University of Applied Sciences Emden/Leer the teams in Leer and Bremerhaven are focusing on wind propulsion systems, design concepts, and scientific studies for emission-free shipping.
The SMM working group provides system-independent research and consulting services spanning all discussed wind propulsion systems for the commercial shipping industry. The spectrum ranges from Flettner rotors, wing rigs, and DynaRigs to membrane sails and classic cloth sails. The Maritime Experimental Center in Leer is at the core of the experimental field.
The unique test infrastructures of the other IWES sites complement the validation options up to full scale. The many years of experience in the field of offshore wind energy create synergies in the working group.
The joint methodological focal points are in the fields of maritime hydro- and aerodynamics, automation and systems technology, and materials technology. Hybrid model concepts result from the intersection of powerful modeling and simulation with measurement technology both in the laboratory and at sea. One special joint area of expertise lies in the utilization of crossover and upscaling effects between wind propulsion technology for vessels and classic wind energy systems.