Joint project simulates wind and wave loads on the piles of offshore wind turbines
A joint project between the LUH and Fraunhofer IWES together with other partners is examining the properties of the current and next generation of offshore monopiles in order to develop a reliable calculation method to enable the longest possible service life.
BMWi-funded joint project: Spectacular pilot project under real conditions at the Test Center for Support Structures of the Leibniz University Hannover
The support structures of offshore wind turbines, in most cases large steel tubes (monopiles), are subject to huge loads from the wind, waves, and sea currents. A joint project between the Leibniz University Hannover (LUH) and the Fraunhofer Institute for Wind Energy Systems IWES together with other partners is examining the properties of the current and next generation of offshore monopiles. These results are then used to develop a reliable calculation method to enable the longest possible service life. The Federal Ministry for Economic Affairs and Energy (BMWi) is funding the Ho-Pile project (investigations into the horizontal load-bearing behavior of XL monopiles under cyclic loading, grant no 0324331) to the tune of around €1,675,000.
In order to replicate offshore conditions, scientists filled the ten-meter deep geotechnical test pit at the Test Center Support Structures Hanover (TTH) of LUH under defined conditions with sand that has typical offshore properties in terms of structure and grain size. The water level was then raised to the upper edge of the sand. “Reproducible offshore-like conditions as well as realistic relationships between soil and pile stiffnesses are important in order to ensure a reliable database for model validation later on”, explained Severin Spill, the project manager at the Fraunhofer IWES. Over the past months, 3 piles have been driven into the soil with a diameter of up to 1.50 m and an embedment length of 6.15 m. On this large scale of 1:5, such tests conducted under controllable realistic conditions are unique in Europe.
The cyclical and static load tests on the model piles are now getting underway. To this end, a steel tube tower has been mounted on the installed piles. A hydraulic cylinder which is secured horizontally to the tower head simulates the relevant load situation. The soil and structural behavior were analyzed and assessed during installation and now again during pile testing. The aim is to develop a validated calculation approach which contributes to the longest possible operationally safe life span of at least 20 years while improving the cost efficiency of the support structure.
Today, a different calculation basis is used in virtually every offshore project. Often the calculations are based on methods which were originally developed for the oil and gas industry. These, however, cannot be transferred readily since the monopiles of offshore wind turbines normally have considerably larger dimensions and are subject to greater dynamic loads. “At the same time, the technical requirements are growing due to ever-larger wind turbines and increasing water depths together with challenging soil conditions”, explained the overall project manager Dr.-Ing. Florian tom Wörden from the Institute of Geotechnical Engineering at Leibniz University Hannover and Dr.-Ing. Mareike Collmann from the TTH. Since a large share of the costs of an offshore wind turbine can be attributed to the foundation structure, an improved design approach will serve directly to reduce the overall costs of energy generation.
The focus of investigations at the TTH is on the impact of the horizontal wind and wave loads which constantly act on the monopile in a cyclical manner. The results will be the basis for the further development of advanced numerical models which can be used in industrial applications. A universally valid calculation approach which enables a more reliable and more economic monopile design is to be developed. The Ho-Pile project is based on the earlier TANDEM project (BMWI grant no 0325841) and will initially run through to November 2021. In addition to the Fraunhofer IWES and the Leibniz University Hannover (Test Center for Support Structures Hanover and the Institute of Geotechnical Engineering), the following project partners are also involved without funding: Jörss-Blunck-Ordemann GmbH, Hamburg, the Federal Waterways Engineering and Research Institute, Hamburg, and the DEWI-OCC Offshore and Certification Centre GmbH, Cuxhaven.
____
Note to editors:
For further information please contact Severin Spill, Fraunhofer Institute for Wind Energy Systems IWES, Department of Support Structures, +49 471 14290-574 or by E-mail at severin.spill@iwes.fraunhofer.de and Dr.-Ing. Florian tom Wörden, Leibniz University Hannover, Institute of Geotechnical Engineering is available on +49 511 762 3735 or by E-mail at tom.woerden@igth.uni-hannover.de.
____
Fraunhofer IWES ensures investments in technological developments in the field of wind energy and hydrogen technology through its validation services. By operating large test rigs, it accelerates the market introduction of innovative products, enhances certification processes and increases planning security by using state-of-the-art measurement techniques. Fraunhofer IWES employs around 250 scientists and administrative staff and more than 100 students at five sites: Bremerhaven, Hanover, Bremen, Hamburg and Oldenburg.
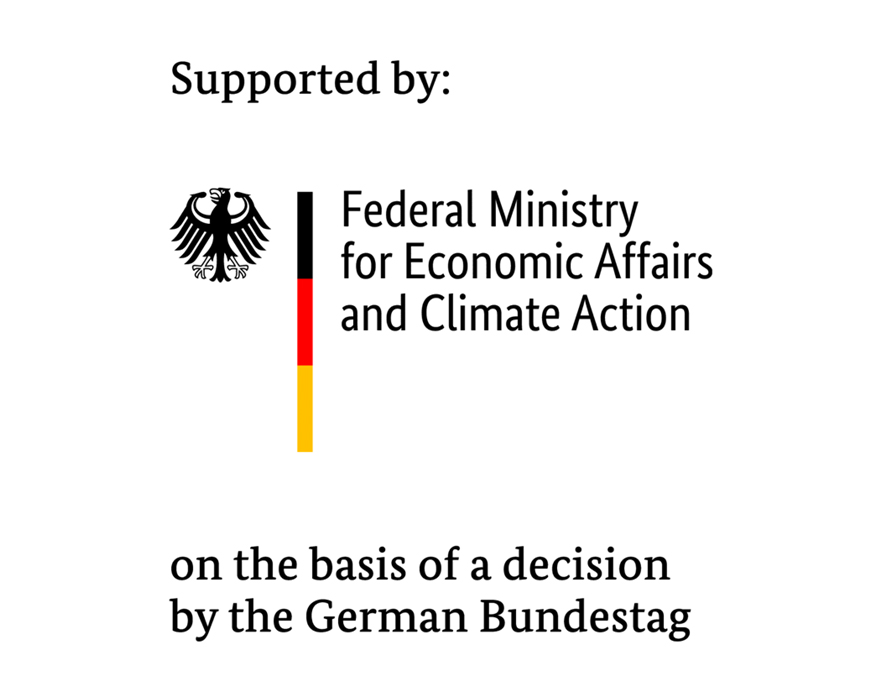
Last modified: